What are the quality advantages of laser quenching?
Laser quenching is a quenching technique that uses laser to heat the surface of the raw material above the change point, thereby hardening the surface of the raw material. So what quality advantages and technical characteristics does it have?
1. Quality advantages
Laser quenching has high power, faster cooling speed, and no cooling materials such as water or oil. It is a clean and rapid quenching process. Compared with the processing technology of induction hardening, flame quenching and nitriding quenching, the laser quenching hardened layer is symmetrical, high in strength (generally 1-3HRC higher than induction hardening), the deformation of the workpiece is small, and the deep heating layer and heating motion track are very easy to manipulate , It is convenient to complete the automation technology. It is not necessary to design the relative magnetic induction electromagnetic coil based on different parts specifications like induction hardening. The production and processing of large and medium-sized parts does not have to be subject to the limitation of the furnace specifications during the organic chemical heat treatment process such as nitriding and quenching. Therefore, in many industrial production industries, traditional handicrafts such as induction hardening and organic chemical heat treatment are gradually replaced. The most important thing is that the deformation of the left and right workpieces before and after laser quenching can basically be ignored, so it is very suitable for solving the surface of high-precision parts.
2. Technical characteristics
The main parameters of the deep layer of the laser hardened layer are in accordance with the components, specifications and appearances of the parts and the laser processing technology, and their main parameters are generally in the middle of the range of 0.3 to 2.0 mm. The shaft journals of large and medium-sized transmission gears and the motor shafts of large and medium-sized shaft parts are quenched. The surface roughness basis will not change, and the requirements of specific working conditions can be considered without post-machining and manufacturing.
Laser melting and quenching technology is the use of laser beams to heat the surface of the sheet above the melting temperature. Because of the heat transfer and cooling inside the sheet, the surface of the molten layer is rapidly cooled and the crystals are condensed. The obtained fusion quenching mechanism is very high-density, and the mechanisms along the deep layer are the fusion-condensation layer, the changed hard bottom layer, the thermally hazardous area and the plate. The laser melting layer is deeper than the laser hardened layer, the intensity is higher, and the wear resistance is stronger. The deficiency of this technology depends on the surface roughness of the workpiece surface suffering a certain level of damage, and generally must be repaired after machining. In order to reduce laser melting. To solve the surface roughness of the surface of the parts afterwards, reduce the output afterwards, and configure professional laser fusion quenching architectural coatings, which can greatly reduce the surface roughness of the fused layer. Nowadays, the hot-rolled strip steel, guide and guard and other workpieces of various raw materials in the industry where laser melting is carried out, the surface roughness has already been close to the level of laser quenching.
The above-mentioned professional knowledge on the quality and technical aspects of laser hardening will be helpful to many interested people.
1. Quality advantages
Laser quenching has high power, faster cooling speed, and no cooling materials such as water or oil. It is a clean and rapid quenching process. Compared with the processing technology of induction hardening, flame quenching and nitriding quenching, the laser quenching hardened layer is symmetrical, high in strength (generally 1-3HRC higher than induction hardening), the deformation of the workpiece is small, and the deep heating layer and heating motion track are very easy to manipulate , It is convenient to complete the automation technology. It is not necessary to design the relative magnetic induction electromagnetic coil based on different parts specifications like induction hardening. The production and processing of large and medium-sized parts does not have to be subject to the limitation of the furnace specifications during the organic chemical heat treatment process such as nitriding and quenching. Therefore, in many industrial production industries, traditional handicrafts such as induction hardening and organic chemical heat treatment are gradually replaced. The most important thing is that the deformation of the left and right workpieces before and after laser quenching can basically be ignored, so it is very suitable for solving the surface of high-precision parts.
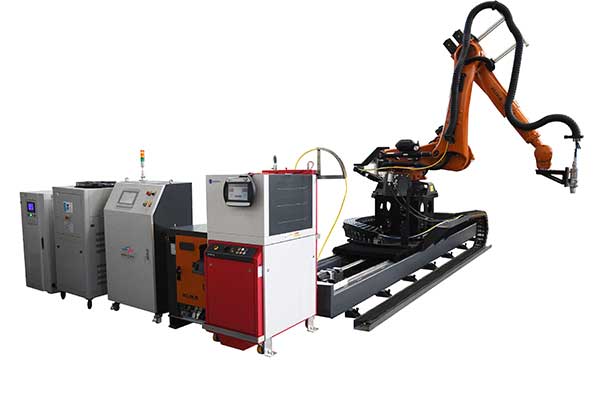
2. Technical characteristics
The main parameters of the deep layer of the laser hardened layer are in accordance with the components, specifications and appearances of the parts and the laser processing technology, and their main parameters are generally in the middle of the range of 0.3 to 2.0 mm. The shaft journals of large and medium-sized transmission gears and the motor shafts of large and medium-sized shaft parts are quenched. The surface roughness basis will not change, and the requirements of specific working conditions can be considered without post-machining and manufacturing.
Laser melting and quenching technology is the use of laser beams to heat the surface of the sheet above the melting temperature. Because of the heat transfer and cooling inside the sheet, the surface of the molten layer is rapidly cooled and the crystals are condensed. The obtained fusion quenching mechanism is very high-density, and the mechanisms along the deep layer are the fusion-condensation layer, the changed hard bottom layer, the thermally hazardous area and the plate. The laser melting layer is deeper than the laser hardened layer, the intensity is higher, and the wear resistance is stronger. The deficiency of this technology depends on the surface roughness of the workpiece surface suffering a certain level of damage, and generally must be repaired after machining. In order to reduce laser melting. To solve the surface roughness of the surface of the parts afterwards, reduce the output afterwards, and configure professional laser fusion quenching architectural coatings, which can greatly reduce the surface roughness of the fused layer. Nowadays, the hot-rolled strip steel, guide and guard and other workpieces of various raw materials in the industry where laser melting is carried out, the surface roughness has already been close to the level of laser quenching.
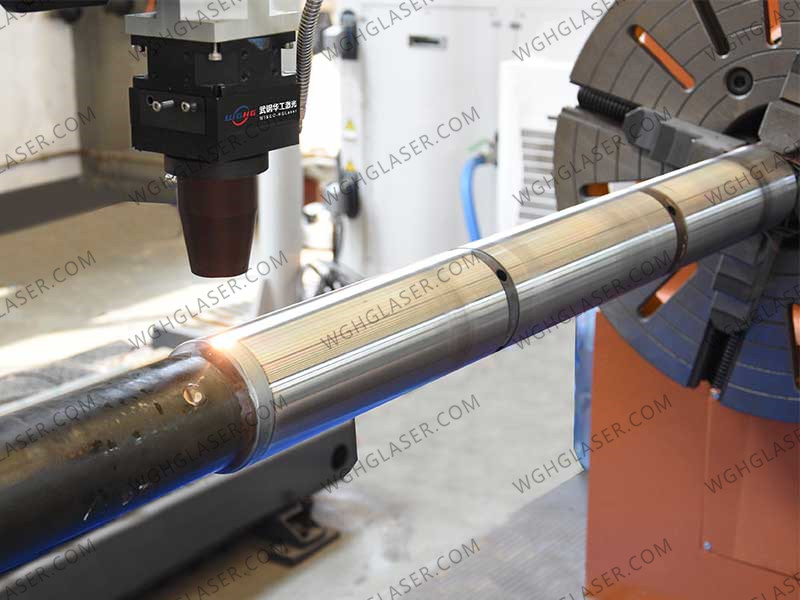